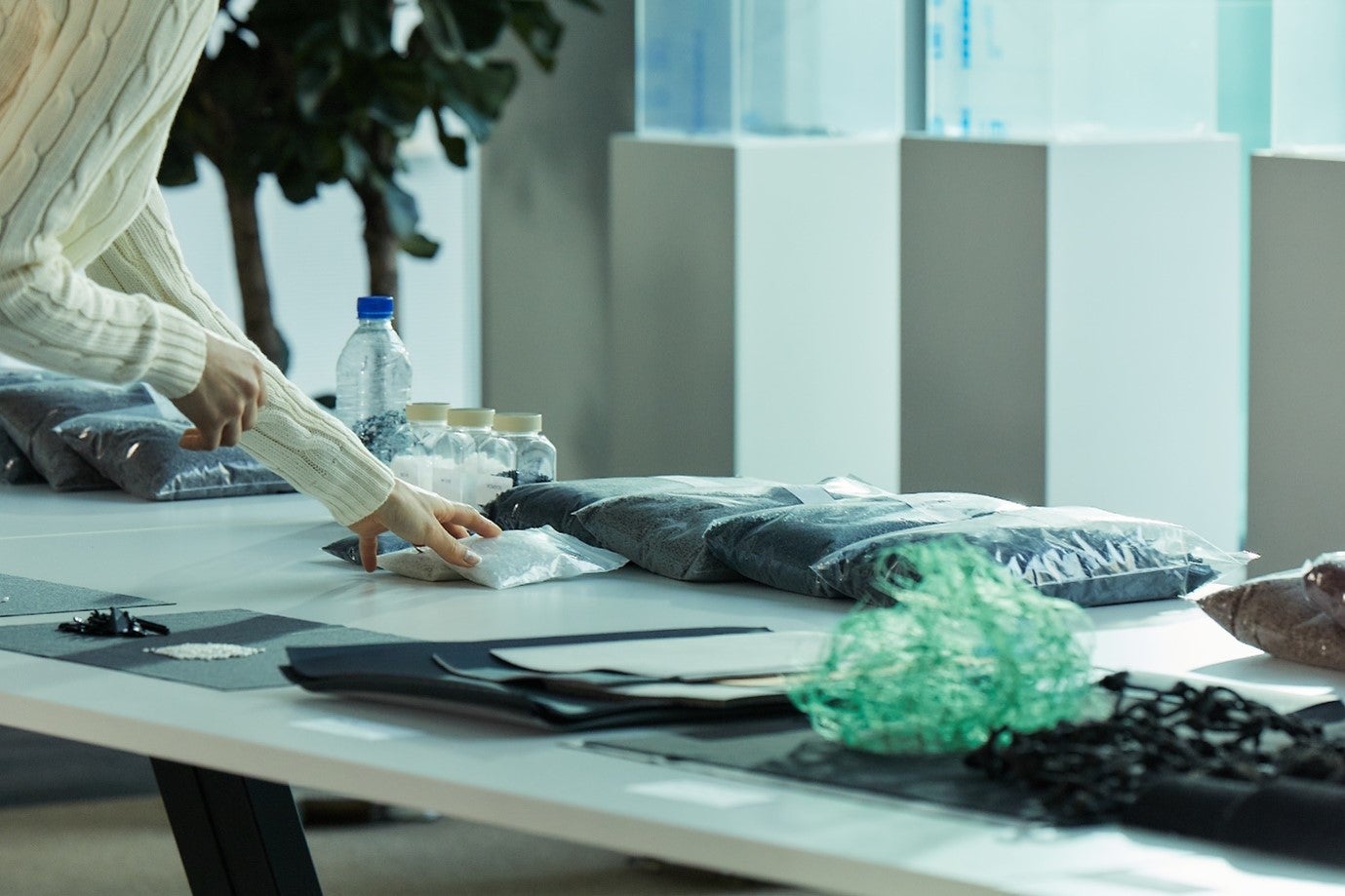
Simulation technology is widely used across the automotive industry from product simulation to ADAS development and crash testing scenarios. Engineering simulation company, Ansys, has been utilising simulation technology to help turn recycled plastic into functioning automotive parts.
By using simulation of materials early on in the design process, it is claimed automotive designers can better evaluate materials for design use, including material variability. This in turns helps reduce cost and time. According to ANSYS, the simulation process enables the simulation of a material hundreds of times to understand the design’s performance and variability, simply by running the same file repeatedly.
We spoke to Donna Dykeman, director and program manager, collaborative R&D, Ansys UK Ltd, and Scott Wilkins, lead product marketing manager, Ansys, to learn more about the process and what it means for the automotive industry.
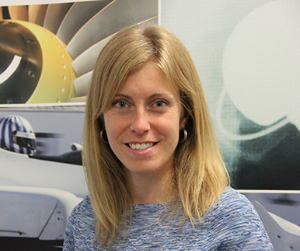
Just Auto (JA): Could you provide some background on the company?
Donna Dykeman (DD): As a business, we often introduce ourselves as a multi physics simulation company. Ansys really has grown up over the past fifty years, in terms of building up digitalising and coding, the raw physics behind engineering applications – and that goes with the physics of materials use as well.
Ansys cover everything from mechanical aspects, fluids, thermal, but also electronics as well and we’re getting into a lot of exciting areas like semiconductors, additive manufacturing, the list could go on – but multi-physics simulation is the premise for it all.
How well do you really know your competitors?
Access the most comprehensive Company Profiles on the market, powered by GlobalData. Save hours of research. Gain competitive edge.

Thank you!
Your download email will arrive shortly
Not ready to buy yet? Download a free sample
We are confident about the unique quality of our Company Profiles. However, we want you to make the most beneficial decision for your business, so we offer a free sample that you can download by submitting the below form
By GlobalDataScott Wilkins (SW): The tagline that we use is powering innovation that drives human advancement. I think that encapsulates what this company is about.
Simulation has become a prerequisite for every engineering business. I think that stems from digitalisation; it’s the exciting thing that you see when you’re within the company and our customers are seeing what you can now do and accomplished digitally.
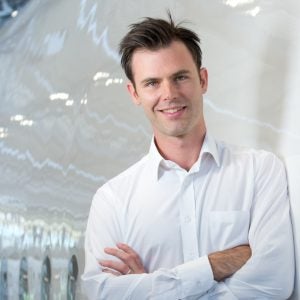
That’s really our space: How we can translate the laws of physics into something that you can visualise and accomplish digitally. That is our power from a company standpoint.
Our customers need that and they need to be able to accomplish this for a number of reasons. They want to get highly complex products to market as quickly as possible. Simulation is one of the enabling engineering tools alongside CAD, and it is starting to become really ingrained.
Using these techniques very early in design is vital; we can impact the whole design in the future if there is that early involvement. It makes the whole process far more efficient.
What is the process of turning recycled plastics into automotive parts?
DD: One of the advancements in in the last few years is to be able to generalise and propagate the variability of a material property. That’s a key advancement that we have in our software and particularly in the physics models that we use.
Using these techniques very early in design is vital; we can impact the whole design in the future if there is that early involvement.
Traditionally engineers produce what would be called a ‘deterministic method’. What that means is you take a single value and you might take another maximum expected value. When we work with the randomness of the material, we’re looking at that material value plus all the parameters and it can have several standard deviations; that is absolutely key for using a recycled material or highly variable material in the design.
Recycled materials have special challenges, especially if you’re going to take them from municipal waste, which is what we have done with several projects. With contamination you may have multiple grades, you may even have life-cycles where the materials have been chopped.
Another example of materials that are high variability are natural materials and biomaterials where there’s a big push around packaging. All industries in Europe are trying to get more biomaterials in products, with a very high percent and have more recycling where possible. You’ve already got a very highly variable material going in there, and then you’re going to recycle it. Handling variability in your design, starting with the material properties is going to be critical going forward.
How can simulation technology and material intelligence assist the industry?
SW: We have the capability to take a very difficult material for a design application. If you can figure out how it is going to act right at the beginning of that design, you can then start to really make it fit into different parts of a vehicle. That’s the bit that hasn’t really ever been done before.
I think we’re at the beginning of this journey over this idea of being able to use not just recycled plastics in this case, but the by-products. To use that and then use it for a vehicle component, I think it’s little bit different, it’s new.
Most vehicle manufacturers, most OEMs, would choose a virgin polymer, because they know exactly how it acts, they know exactly what to expect from that material. This brings into question for the designer right at the beginning of that vehicle’s life and the part being considered – should they be using a virgin polymer, or should they be using recycled material? We can show how the recycled material behaves, how they can now design with it, what the properties are going to be because we can narrow down accurately to see what the recycled material can do and how it performs.
DD: It really benefits automotive companies in terms of lowering risks; it saves you on time, saves on cost. The result is you can simulate over and over again using one representation; you have that material card, you have that one digital representation, and you just repeat use it over again.
In an example of say 100 parts manufactured from this card, the randomised material cards can be simulated 100 times, whereas traditionally you’d have to go out and physically make the part and destroy it each time to get that same representation in the variability. The physical time saved is the big pay-off.
Do you have some examples of where it has been used?
SW: A very good example is Red Bull Racing. They were in the very first episode of ‘Driven by Simulation’, which is a TV docu-series. One of the heads of simulation featured in the episode and they talk about how simulation plays a key role from the fluid dynamics around a Formula One vehicle. The rules for Formula One are changing every year, so you have to very rapidly be able to understand what that little change means to the design of your vehicle. Simulation is a very good way of doing that.
So, fluid dynamics, the mechanical side of things, all the various physical properties, are all deployed in the simulation, along with specialist materials, too. Materials are a component that they talk about in in that video.
Our customers really span OEMs, Tier 1, Tier 2 and all the way through the supply chain. We’ve got a very good coverage of a wide variety of automotive customers and that includes Red Bull and Porsche racing. We have a number of different customers that use our technology, and externally we have had Lamborghini and Ferrari use our materials management software.
Materials are a key input into any simulation. You need to understand your material
Materials are a key input into any simulation. You need to understand your material. If you have the right material properties and if you’ve got accuracy behind the material properties, then that will translate to an accurate simulation. So being able to manage what that material is, where it is, who’s using it across the business becomes pretty important to people.
What does this mean for the future of the automotive industry?
DD: So you know, we’ve talked a lot about like OEMs; you know, they’re the people who are taking all the parts together and assembling them. But really, what this type of analysis allows you to do is to test materials in a virtual environment and go back to the suppliers and say ‘no, this isn’t good enough, I need my variability to shrink by a certain amount or I need to shift my string up a little bit better, to get it to get the results that I need’.
It’s about being able to test in the simulations to get the best results with materials and design. Whether its CO2 or safety performance – eg crash scenarios – there are lots of potential scenarios, iterations and simulations to potentially generate. You can optimise with a recycling supplier to say, look, in order to push this down into a competitive overlay with these other ones, you have to shrink your variability by 1.5% standard deviation or you need to increase your yield strength. Then they can go back and tweak things – say the additives or they could do more blending. They can maybe extract one of the grades that maybe isn’t helping you especially in the polymer; they can do all sorts of things.
So we see these types of workflows, really connecting the supply chain together and working in a virtual environment together, very iterative. I think that’s going to be a critical next step.
SW: And in three years’ time, the workflow could have been refined, the material could have been refined, too. We think the whole concept of being able to use recycled materials will become much more prevalent. If automotive designers know that in the future you don’t need to use virgin polymers, you can use recycled materials, they will know the properties that it will have and will be able to put that into a computer model. You can use that as part of your simulation.
You can start to imagine that the chassis of a vehicle, or the components of a vehicle, are starting to change with the greater understanding of those recycled material properties. Today it’s maybe designed with an aluminium part and it has been an aluminium part for the last twenty years. Maybe it won’t be in the future and will, instead, be a recycled material.
We know that we can make that and the design engineers know that they can use that, and make it cost effectively because of this process. At the moment, it’s still a case of putting all these tools together in the workflow; this is a combination of multiple tools that are being used in conjunction which is not easy. We have got some very smart people who are going to figure it out and say: “This is how we use these various simulation tools in conjunction to be able to take this material, do crash testing on it, optimise and create this workflow.”
In the future we will have a range of new materials across the supply chain that will be ready to be used. There will also be a new philosophy on how to potentially design the vehicle so that it will adopt more recycled content, giving a real boost to the idea of the truly circular economy in automotive manufacturing.
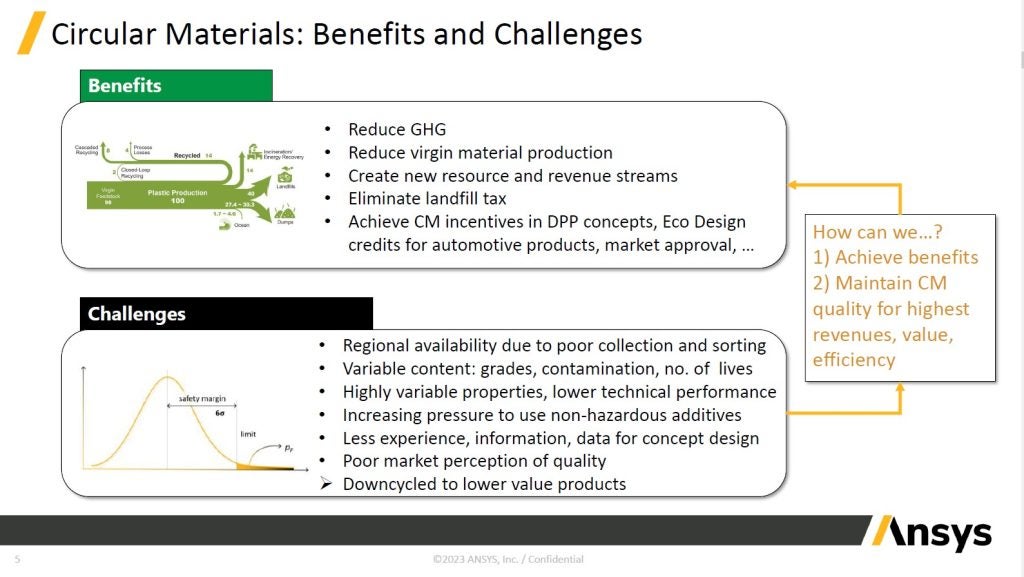