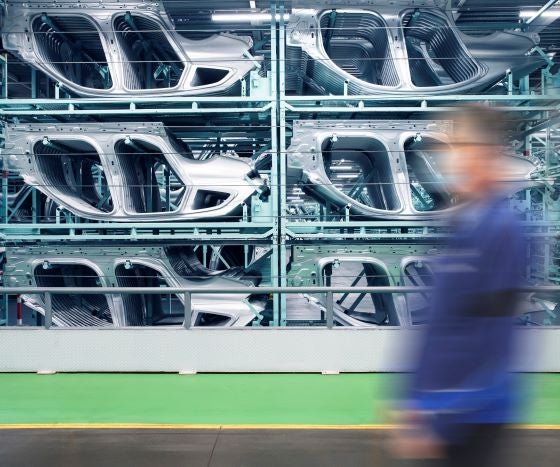
Material matters
For some time, the automotive industry has been under pressure to change the way it designs and builds vehicles, due to factors such as the increasing impact of passenger and pedestrian safety requirements and the competitive intensity caused by globalisation and manufacturing in low-cost economies.
Governmental pressure worldwide to reduce CO2 emissions has also prompted automakers and their supply base to develop automotive technology to meet those strict emission limits. Consequently, more and more vehicles are incorporating components aimed at a mass reduction, parts consolidation to reduce assembly costs and more efficient recycling. The automaker’s need to improve overall fuel economy in vehicles has led to the trend toward minimising vehicle weight using a blend of high-strength steel and aluminium.
Steel focus
Launched in 2018, the e-Niro is Kia‘s second globally sold electric vehicle after the Soul EV. Made up of 53 per cent advanced high-strength steel, the e-Niro’s structure is particularly strong. It also has liberal doses of aluminium. Its bonnet, tailgate panel, front bumper back beam and several chassis elements, including the front knuckles, front lower arms and brake calipers are made of aluminium to further help reduce weight. The lightweighting theme spreads into the interior as the front seats save 1.3kg each thanks to their high-strength steel frames. The shapely front seats are also space-saving with special foam-backed covers and slim headrests. A tyre mobility kit was found in the boot rather than a spare wheel, reducing weight yet further.
The third generation Kia Soul is powered in Europe exclusively by electric energy. With a claimed combined range of 280 miles on a single charge, that’s a country mile improvement on the original Soul EV’s 132 miles and should relieve any symptoms of range anxiety. The longer range is due partly to the knowledge the Korean carmaker has gleaned from its e-Niro. The Soul EV makes good use of high-strength steel in critical areas. Its body is made up of a blend of steel and aluminium, maximising torsional rigidity while keeping body weight low. With a higher proportion of advanced high-strength steel and hot-stamped steel components than its predecessor, as well as new aluminium side-sill reinforcements, the more rigid body shell reduces road vibrations and enhances occupant safety in the event of a collision.
How well do you really know your competitors?
Access the most comprehensive Company Profiles on the market, powered by GlobalData. Save hours of research. Gain competitive edge.

Thank you!
Your download email will arrive shortly
Not ready to buy yet? Download a free sample
We are confident about the unique quality of our Company Profiles. However, we want you to make the most beneficial decision for your business, so we offer a free sample that you can download by submitting the below form
By GlobalDataBuilt on a PSA platform, the face-lifted seventh-generation Vauxhall Astra is one of Britain’s top-selling cars. Astra is a household name with over three million sold in the UK over the last four decades. Depending on the model and trim level, the Astra is up to 200kg lighter than its predecessor. The body shell weight alone was reduced by 20 per cent from 357kg to 280kg. More specifically, the seats are smaller and 10kg lighter thanks to some clever packaging methods, lighter polyurethane foams and ultra-high-strength steel frame. The 18-way adjustable front seats are offered with additional comfort features such as side bolster adjustment, massage and memory function along with ventilation.
The hot hatch version of the Suzuki Swift is powered by a canny mild-hybrid set-up. Under the ‘Suzuki Next 100’ plan announced at the IAA in 2015, Suzuki developed a new platform strategy for its future models and in 2018, the Swift Sport was introduced as the fourth model (following Baleno, IGNIS and Swift) to adopt this lightweight platform and be introduced in Europe. Known as “HEARTECT” the lightweight platform delivers enhanced fundamental vehicle performance due to being light and highly rigid. Based on its kerb weight of 1,025kg and a torque figure of 235Nm, the Swift Sport has a torque-to-weight ratio of 4.3 kg/Nm placing it at a similar level to its competitors. The bodyshell includes the use of ultra-high tensile steel (980Mpa) across 17 per cent of its structure and high tensile steel (789 MPa) across four per cent of its structure.
The Honda Civic Type R’s edgy body shape, boy-racer spoiler and outlandish vent-laden front bumper give it an undeniably extroverted road presence. The unibody platform of the tenth-generation Civic means that the Type R’s body frame is 16kg lighter than the previous model, with a torsional stiffness improvement of 37% and a static bending rigidity improvement of 45%.
Lightweight alloys
Following the launch of the Alfa Romeo Giulia, the range was expanded to include the Veloce that fills a gap between the Speciale and flagship Quadrifoglio. To obtain a weight-to-power ratio and torsional rigidity, the Giulia uses an array of high-strength and ultra-lightweight materials including, for example, carbon fibre for the driveshaft, aluminium composite and plastic for the rear cross member and aluminium for the doors, wings, engines (petrol and diesel), brakes and suspensions – including the front suspension domes and front and rear subframes. As a result, the dry weight of the 180hp 2.2-litre turbo diesel version is 1,374kg.
The BMW 4 Series Coupé is undeniably stunning with its sleek silhouette, carved surfaces and swoopy roofline. The body and chassis components feature a mix of steels and alloys to minimise vehicle weight. Underneath, the car uses an engine side member (made from extruded aluminium profiles) and die-cast aluminium spring struts, while the exterior features an aluminium bonnet, front side panels and doors. A material made from natural fibres is used for the boot lid lining.
With its sharp looks and muscular road stance, the Peugeot 508 further distinguishes itself with a finely fashioned radiator grille complete with chrome plated chequerboard. The vertical visual signature of the blade-like LED daytime running lights also catches the eye, framing the car’s front end. Explaining the technical challenges faced in designing the car, Pascal Delabarre, Project Director for the 508, said: “In terms of metal fitting, we introduced a technique for welding body parts that was strengthened with structural adhesive. Certain premium carmakers use this. The method reinforced the body’s rigidity and ensured better acoustic insulation. We also had to systematically shed needless weight. By taking this approach, we got rid of 70 kilos from the car. This was especially challenging due to the heaviness of certain equipment, such as the tailgate motor and the frameless doors. This required radical solutions, for example, hot metal stamping and producing the boot and front wings in aluminium and the tailgate in thermoplastic.”
Weightwatchers
On balance, we can expect a mass-produced car’s body panel and frame construction to continue to be dominated by steel and aluminium and await the gradual addition of lighter metals/alloys.